Integrate your production planning with execution, optimize resources, reduce costs and respond dynamically in real-time.
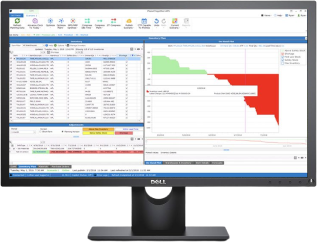
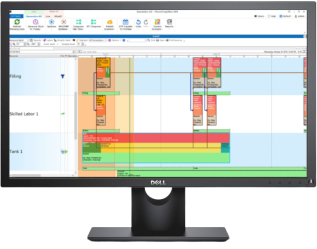
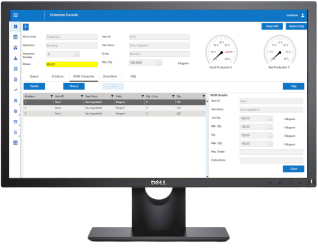
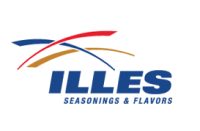
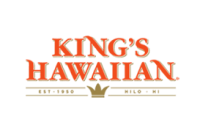

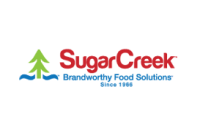

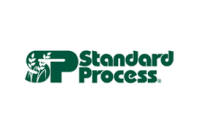
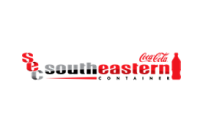
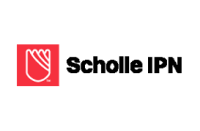
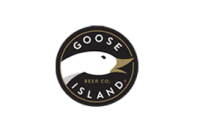
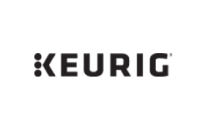
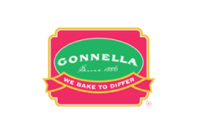
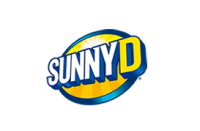
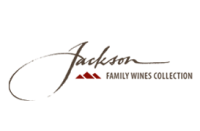

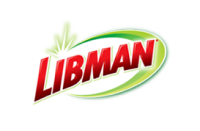
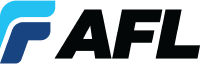
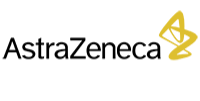

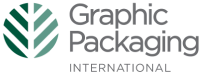

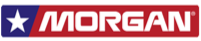
Manual scheduling tools and outdated methods lead to inefficiencies, unnecessary changeovers, delays, and high costs. Here’s what might be holding you back:
From minimizing disruptions to optimizing resource allocation, PlanetTogether APS addresses real-world manufacturing challenges effectively
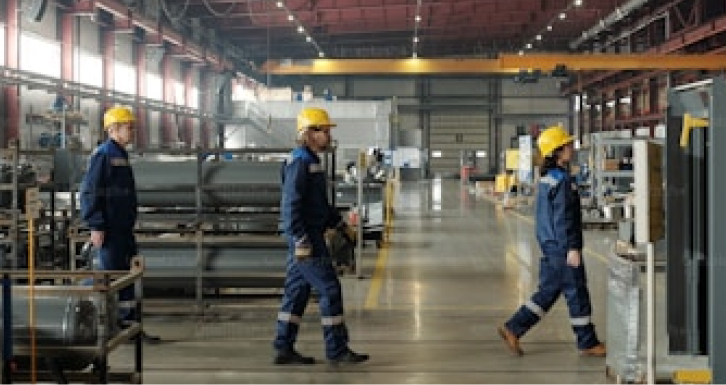
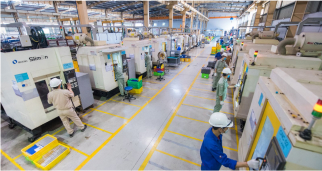
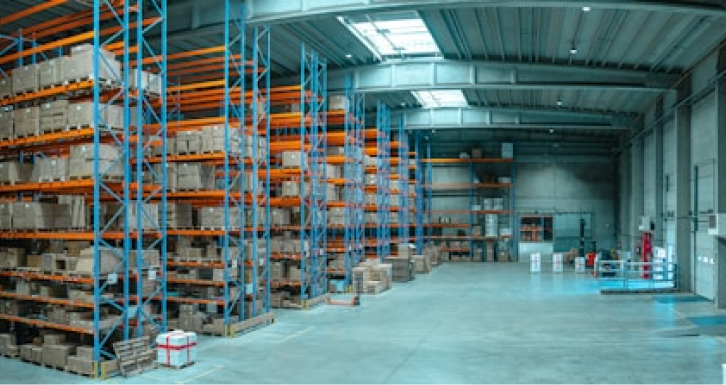
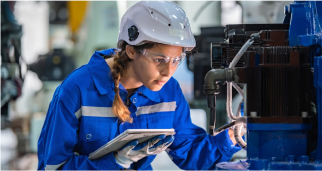
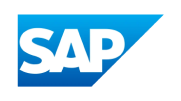
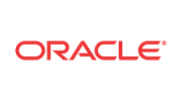
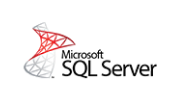
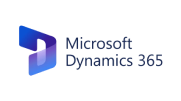
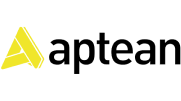
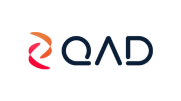
How PlanetTogether Benefits Your Entire Team

Operations


Service

Scheduler


Planner
PlanetTogether APS tackles each stage of the manufacturing value chain, from raw materials to final delivery, with advanced features that provide real-time adaptability, visibility, and control over every production variable.

“The shift to PlanetTogether is saving us about 15
percent in inventory overhead and about 20 percent in
overtime labor expenses. We’re not building equipment
to stock any longer—we’re building to ship!”
Director of Manufacturing,
DePuy Synthes, a Johnson & Johnson Company

How long does it take to implement PlanetTogether APS?
Immediately. AVEVA Customer FIRST is not just a cliché, it is a mantra that drives our everyday efforts to put our customers first – ensuring their overall success with our software is essential. We strive to deliver innovative, market-leading software coupled with a wide range of services and resources.
Does APS support multi-site manufacturing?
Absolutely, with our SuperPlant™ feature, you can synchronize schedules across all locations.
Does APS integrate with basic ERP systems?
Yes, PlanetTogether APS integrates seamlessly, replacing manual scheduling tools.
What ROI can I expect?
Most clients see measurable improvements within one year, including cost savings and delivery performance.
What prerequisites should a company meet internally before installing APS?
APS is a “data-intensive” tool requiring the right information to be accurate. Fortunately, most companies already have 99% of the data needed to get started and you can improve it over time. One benefit of an APS system is that it provides an incentive to clean-up and standardize data that was previously under-utilized and somewhat neglected.
You’ll need routings and bills-of-material for discrete manufacturers or formulas and run-rates for process-manufacturers. For inventory-constrained scheduling, it’s also important to have a reliable inventory control process with accurate on-hand quantities. Also, if you follow a daily planning cycle, you’ll need to track production completions daily, as well; if weekly, then production updates can be tracked weekly.
We're not sure if we need "finite" scheduling. When is finite better than infinite?
While rough-cut infinite capacity planning is useful for planning labor and capacity levels long-term, most manufacturers find it far more value to use finite constraint-based planning. Unless you plan to schedule a very low volume of production orders (maybe 25) and can manually make drag-and-drop adjustments, finite scheduling will deliver many benefits infinite planning will not. Even if you have enough capacity on average, there are likely “clumps” of workload that will create temporary bottlenecks. Finite scheduling gives you the insight of where and when theses bottlenecks will occur. And you understand the impact of these changes on the order schedule, which enables you to produce detailed, actionable plans that invariably save valuable time on the shop floor and planning department.
Why do we need an APS tool if we already have an ERP system?
ERP systems are ideal in managing transactions, like order entry or inventory control. ERP evolved from accounting systems to keep track of what has happened versus planning for what is going to happen. As a result, the architecture is optimized for transaction processing rather than large-scale, high-volume data analytics. Consider a typical MRP re-gen can take hours or days while an APS re-gen usually takes a few seconds. This is a critical usability factor because no planner can afford to wait hours, let alone days, after every schedule change.
Better still, the design and development expertise in an APS system is unique and specialized, and hard to come by. Most ERP development projects leave planning as an afterthought and only address it superficially. APS is all about the details. That’s why most “classic” scheduling in ERP systems goes unused; it is too simplistic to affect real improvement. APS solves critical problems and drives productivity.





